Drone Motor Introduction
Understanding the specifications of drone motors and how they work is important for any hobbyist. There may come a time when you will want to replace a burned-out motor, upgrade your existing drone motors, or even build a drone. This article serves to help you understand the basics of drone motors so you can pick the best drone motor that meets your requirements and budget.
If you google drone motors, you will come across many articles on this topic. However, I find that most of these simply gloss over the explanation, and only provide a surface level explanation. Hopefully, you will find this article much more informative.
The Starting Point – Drone Weight and Frame Size
There are two parameters that determine the drone motor size for your quadcopter:
1. Your quadcopter total weight
2. Your quadcopter frame size
If you are building your drone, you may not know the final weight. However, you can determine the final weight by considering the weight of all of the individual components.
The frame size will let you determine the proper propeller size to use.
Once you know the propeller size and the weight of the drone, you can determine how much thrust the individual drone motor needs to generate to get your quadcopter into the air.
Drone Motor Thrust to Weight Ratio
The thrust to weight ratio TWR = T / W is the main dynamic characteristic that will determine your drone flight profile. To maintain steady flight, your TWR needs to be equal to one (see Figure 1). However, to take off you will need TWR > 1 so you have a net acceleration upwards. When flying, the angle of attack of the drone (ie the tilt angle alpha in Figure 2) causes the thrust vector to have vertical and horizontal components. This requires the TWR to be at least 1.3 for an approximate maximum angle of attack of 40 degrees.
A general rule of thumb is that the drone motors should be able to provide twice as much thrust as the weight of the drone. If the thrust provided by the motors is too little, you will experience poor flight performance. If you have 4

Fig 1. Thrust vs Gravity
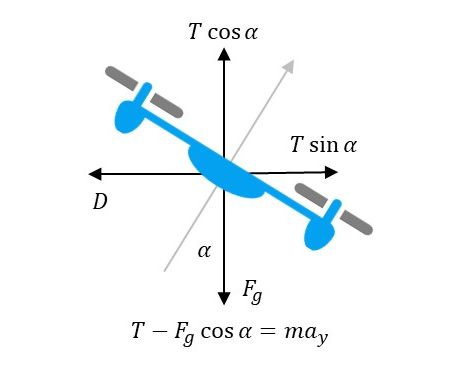
Fig 2. Drone Flight Motion
Drone Frame Size
The size of the propeller that can be used is determined by the frame size. The maximum size of
Figure 3 shows a square drone frame configuration, so the maximum propeller size is X/2.
Figure 4 shows a rectangular frame size so in this case, Y is the obvious minimum dimension, so the maximum propeller size is Y/2.
Overlapping the propellers is not recommended since the downward airflow of one propeller will reduce the thrust efficiency of the propeller below. There is also a bit of side to side airflow due to tip vortices, so you want to allow for some spacing between the propellers to avoid this effect.
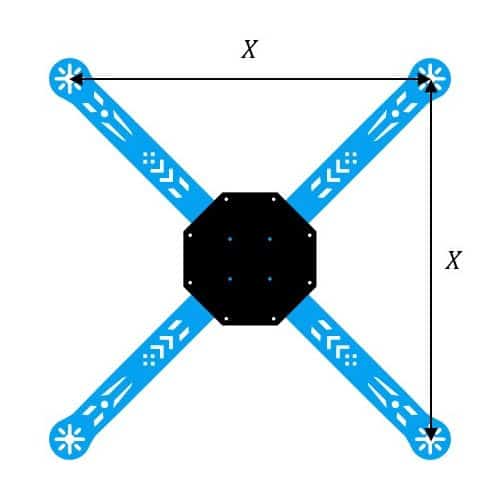
Fig 3. Frame and Prop Size
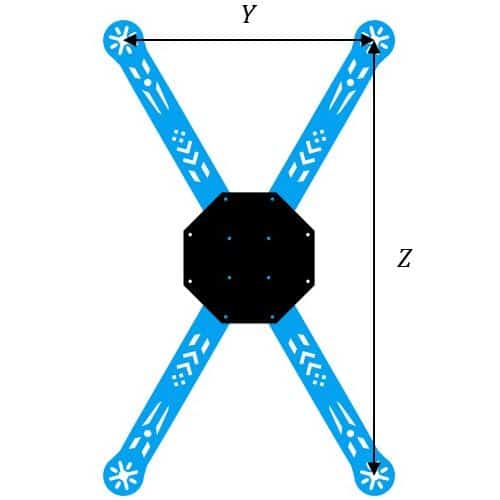
Fig 4. Minimum Frame and Prop Size
Drone Motor Size and kV
The size of brushless motors
A taller stator provides more power at higher RPM, while a wider stator provides more torque at lower RPM.
Also, a larger stator height means a bigger permanent magnet size (see Figure 6), while an increased stator width means a larger electromagnetic coil size.
The size of the prop shaft on the motor determines the size of the propeller that can be used. Motors with
The kV motor specification is the number of revolutions per minute that the motor will turn when one volt is applied with no load on the motor. When you attach a propeller, you will get a reduction in the number of RPMs due to
2204 and 2205 are common motors that are used on quadcopters. A good propeller matching for thee motors are:
- 2600 kV and higher motors for 4” propellers
- 2300-2600 kV for 5” propellers
- 2300 kV and lower for 6” propellers
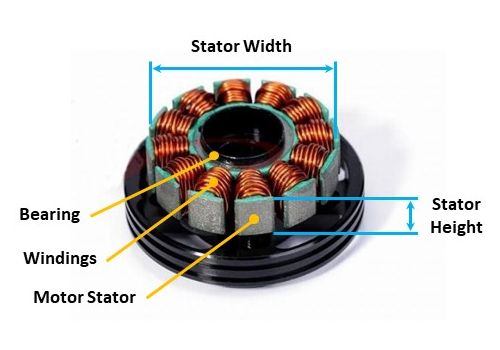
Fig 5. Drone Motor Stators
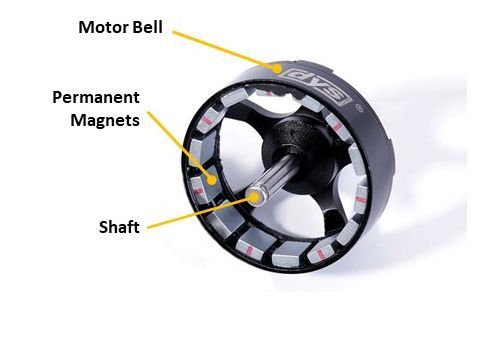
Fig 6. Drone Motor Bell
Drone Motor Efficiency
Electric motor efficiency is the ratio between the mechanical power output and electrical power input. The mechanical power output is determined based on the torque and speed required and the electrical power is determined by the voltage and current supplied to the motor.
However, the motor efficiency is not constant over the entire thrust profile. Some drone motors may be efficient at a lower throttle, but start losing efficiency at higher currents as it approaches its maximum limit. You will be wasting battery energy and drone flight time with less efficient motors.
To get a higher thrust, the motor will need to draw more current. The best combination for a drone motor is high thrust with
Typical drone motor efficiencies have a value of 7.
Drone Motor Torque
The maximum thrust of a given torque motor and propeller combination is achieved when the motor has reached maximum RPM. However, the torque of a motor determines how quickly the motor can vary the speed of the propeller. For example, how fast can the motor rotate the propeller from zero to maximum rpm?
The effect of the motor torque will be noticed when you start flying your drone. If the drone motor torque is too low, the quadcopter can feel sluggish, and slow to respond to commands.
You need to strike a good balance between motor rpm and torque when matching a drone motor with a propeller.
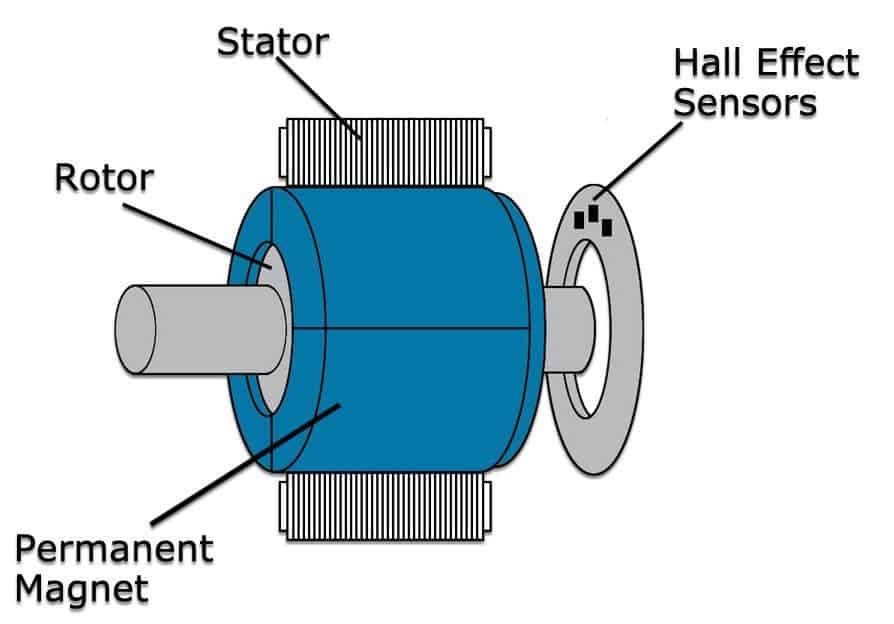
Fig 7. Brushless DC Motor
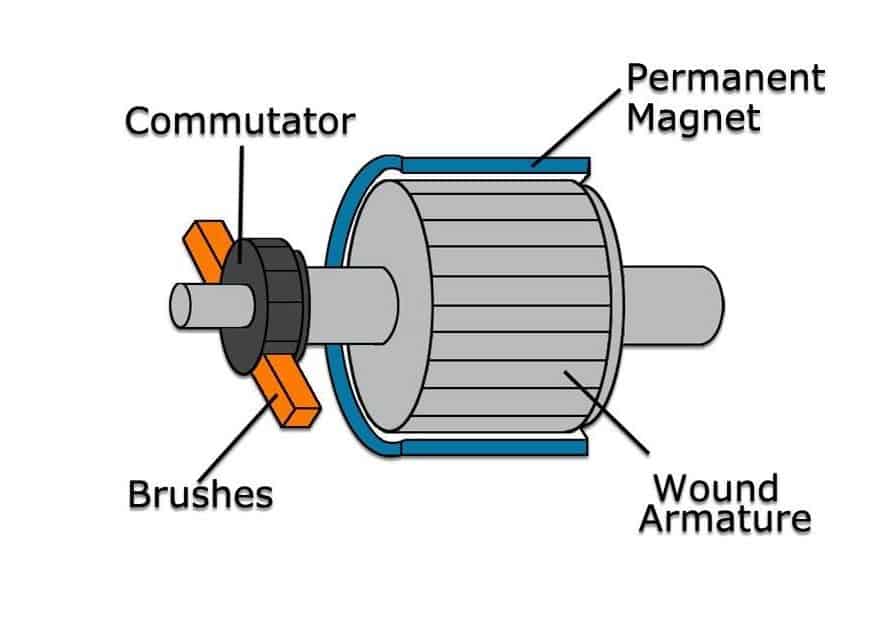
Fig 8. Brushed DC Motor
Drone Motor and Propeller Sizing Example
Even with an understanding of the material previously presented in this article, sizing a drone motor and propeller combination can be somewhat of a difficult task. Fortunately, many drone motor manufacturers provide motor and propeller performance data that makes this sizing task much easier. However, if you do not know how to read the data, it can be confusing.
In this example, we will assume that the frame is 500mm
Figure 9 shows a section of the performance chart for a Cobra CM 2217-20 drone motor. If you look at the line for the prop 12×4.5-MR, you will see that this prop and motor combination produces 1168 grams of thrust. This is close to the needed thrust, so we will use this combination.
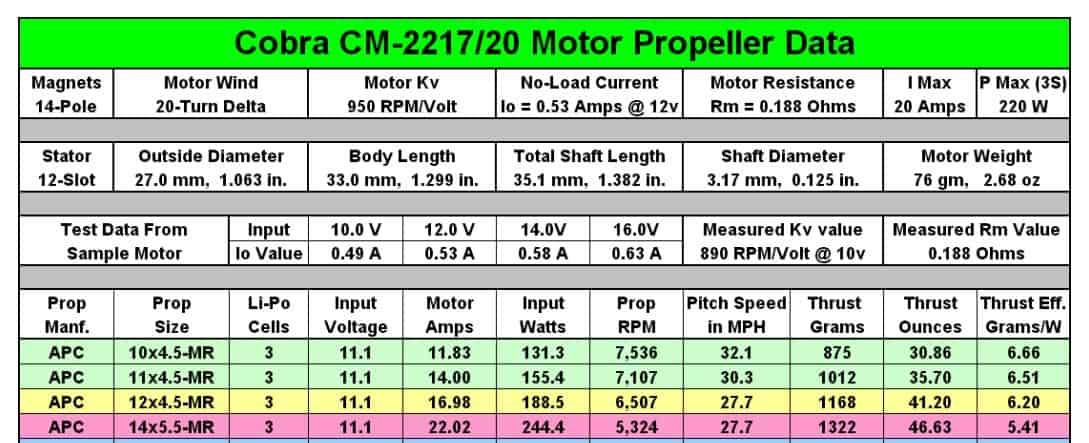
Fig. 9 Motor Propulsion Chart
Once the motor and propeller have been selected, the electronic speed control (ESC) needs to be selected as well. Even though most of the time the drone will be flying in the 40 to 60% throttle range, the ESC needs to be sized to handle the maximum rated motor current in order to handle the occasional full throttle burst. The Cobra CM-2217-20 motor has a maximum current rating of 20 amps, so this the minimum ESC size that should be used. However, its good to add a bit of a buffer so that the ESC is not overworked. In this case, a 25 to 30 amp ESC would be a good size.
Now that the
First, we will look at the Propeller Thrust vs Throttle Position graph to see
Step 1: To determine the throttle setting needed for hover, you use Figure 10.
Step 2: Then draw a light straight down from this intersection point to the x-axis. This point is slightly under the 50% mark, so we will use 49%.
Step 3: Using the Motor Current vs Throttle Position graph (Figure 11), draw a vertical line up from the 49% throttle point until you hit the blue curve.
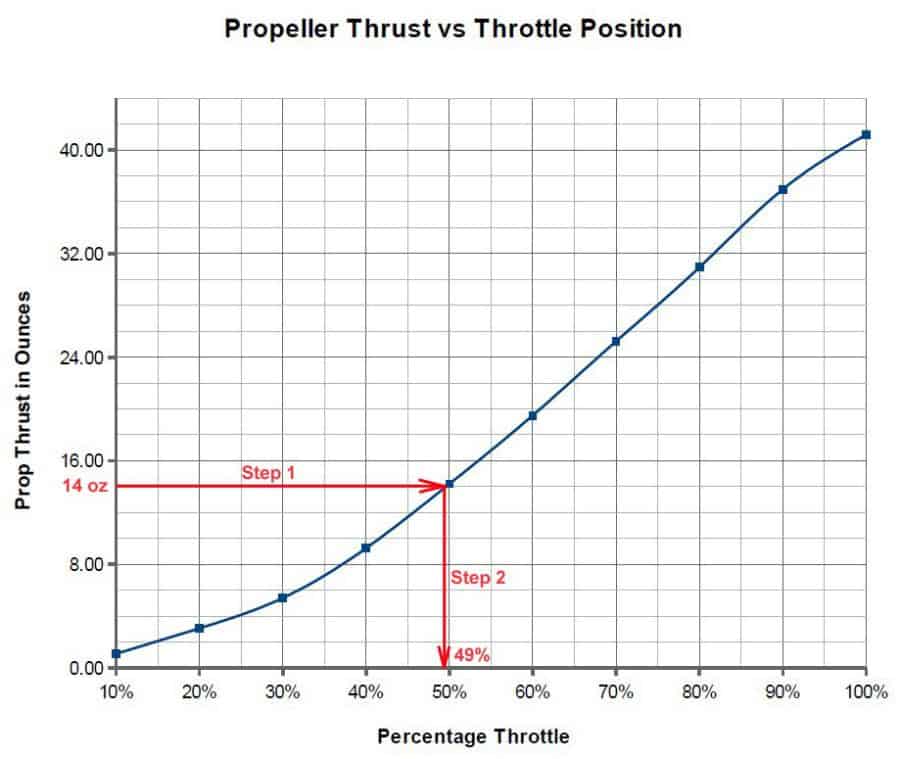
Fig 10. Propeller Thrust vs Throttle Position
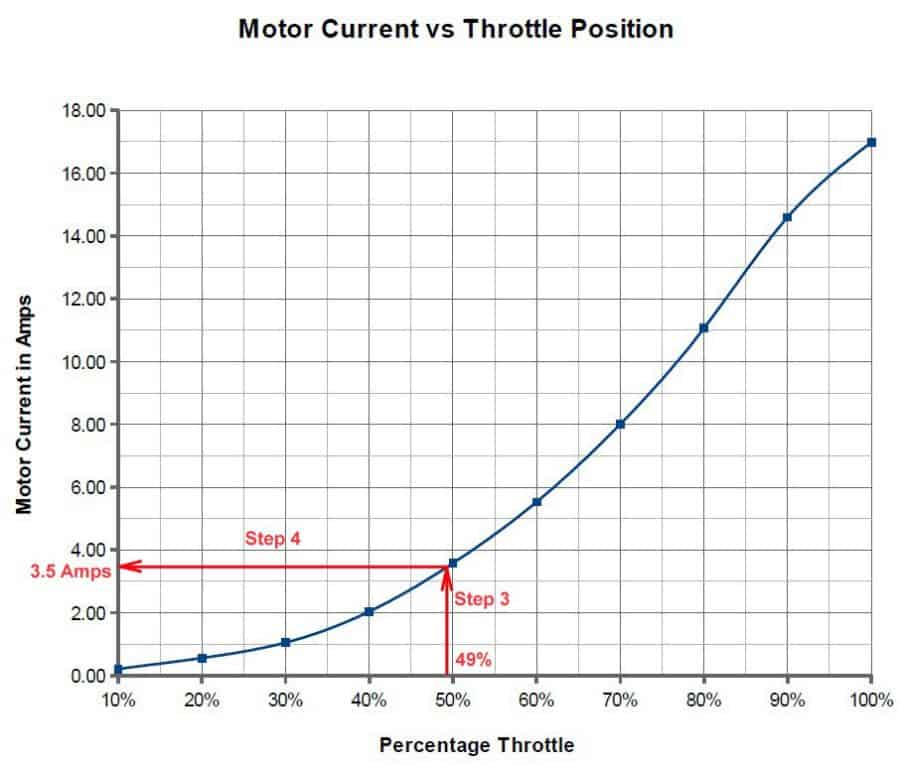
Fig 11. Motor Control vs Throttle Position
Step 4: Draw a horizontal line from this intersection point over to the y-axis. In this example, it is 3.5 amps per motor. Since we have 4 motors, we will need to draw 14 amps from the battery to hover.
We have enough information to be able to determine the approximate flight time of this drone. As indicated earlier, the battery in this example has a 5000 mAh capacity.
Battery discharge is measured in multiples of the C rating, which represents the capacity of the battery. A 1-C discharge rate will drain the battery in one hour. A 2-C discharge rate will drain the battery in 30 minutes. A 3-C discharge rate will drain the battery in 20 minutes. So first we will calculate the C-rate of discharge.
The C-rate of discharge in this example is the battery capacity divided by the current draw 5Ah / 14 amps, or 2.8-C. To calculate the time required to discharge the battery, we divide 60 minutes by the C rating to get 21.4 minutes. You never want to completely drain a LiPo battery, so we will want to be sure to leave 20% charge in the battery. So, we can hover the drone for a maximum time of 17.1 minutes.
Remember, this flight time is only if the drone is hovering. Depending on how you fly, the actual flight time will be less than 17.1 minutes. If you are using the drone for aerial photography, taking 75% of the calculated flight time is a good starting point. So we can expect a flight time of 12.8 minutes.
Drone Motor Summary
In this article, we discussed the various specifications of drone